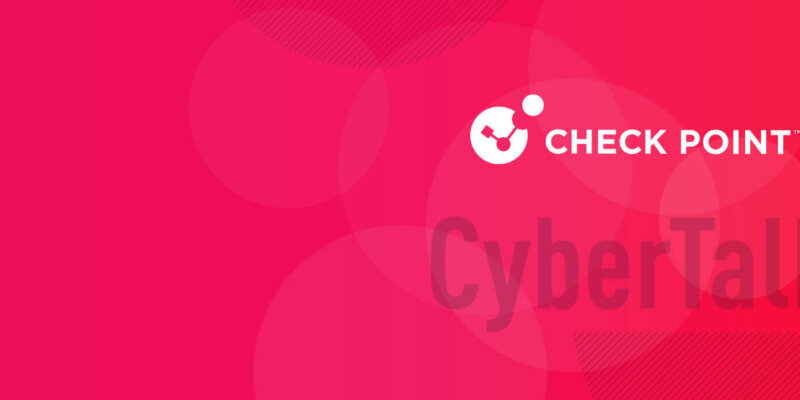
How addressing “Hidden Factory” can boost the transition to “Green Factory”

Antoinette Hodes is a Check Point Solution Architect for the EMEA region and an Evangelist with the Check Point Office of the CTO. She has worked as an engineer in IT for over 25 years and is an experienced Security Solutions Architect with broad experience in the cyber security industry. She is a strong customer advocate who connects people & processes with technology by matching the clients’ business needs with security solutions and services. Antoinette commonly drives meetings within the C-suite and takes a profit-driven approach. Her goal is to support clients with their secure digital transformation journeys. Antoinette is passionate and eager to learn when it comes to technology. Personal mission: Making internet a better place for our children!
In this outstanding interview, Antoinette Hodes discusses the digital transformation from Hidden Factory to a Green Factory. This is a journey that offers manufactures the capability to fully enjoy Industry 4.0 and Industry 5.0 technologies.
What is a Hidden Factory?
The Hidden Factory leads to decreased quality or efficiency of a manufacturer. It encompasses the untapped capacity of the manufacturing plant. It is a set of activities or undocumented processes. The Hidden Factory is, in-essence, the non-visible costs, inefficient processes, and the wasteful operations. The Hidden Factory houses profit reducers and waste increases. Waste is not only measured in terms of money, but also in time, materials and other resources. The term “Hidden Factory” was introduced by Dr. Armand Feigenbaum. More information can be found in this article.
Dr. Armand Feigenbaum states that 20% to 40% of activities in a factory are unplanned. True costs are underestimated in most manufacturer environments. The math is A x P x Q = OEE. Meaning: Overall Equipment Effectiveness = Availability x Performance x Quality.
Traditional manufacturing costs are easy to measure and often clear. However, the Hidden Factory cost are not as easy to understand, as they depend on the vertical that the manufacturer is operating in. The Hidden Factory is “responsible” for late delivery, lost customers, and finally lost sales. We learned that a Hidden Factory rarely refers to just one problem; rather, in reference to Hidden Factory, there are multiple problems impacting the manufacturing operation. The Hidden Factory not only impacts quality and efficiency, but it will also increase cost and decrease customer value. Adequately addressing the Hidden Factory has become more important now given the economic slowdown, immense rise of energy and electricity costs, the chip shortage and inflation.
Benefits of tapping into the Hidden Factory
- Decreased cost and increased profitability
- Increased throughput on existing factory assets
- Increased flexibility and shorter production cycles
- Improved ROI (Return on Investment)
- Happy customer base
- Process improvements
Another driver of runaway manufacturing costs is how to become “green” and “sustainable,” mitigating industrial impact on climate change and other environmental concerns. A green factory is a factory working with fewer resources (i.e.. Energy and materials) to reduce pollution, waste, effective recycling and reuse. A Green Factory has a very low emission and carbon footprint. Basically, it is minimizing damage to the environment. The Green Industrial Policy, the GIP, assists industries in moving towards a low-carbon economy for building a “greener” world.
Becoming a “Green Factory” is all about optimizing big R’s: repetitive processes, ROI, repair, reuse, refurbish, remanufacture, rubbish and recycle.
How to address the Hidden Factory challenge?
Solutions are needed to provide short feedback loops to quickly identify and mitigate upcoming problems and threats. The digital transformation journey from Industry 4.0 to Industry 5.0 will help manufacturers; think of IoT (i.e. smart sensors), Industrial IoT, Edge assets, and AI (i.e. for predictive maintenance). Smart sensors and Smart Edge assets can provide in depth insight, as they can monitor all kind of critical processes throughout the manufacturing process. The technological advantages of Industry 4.0 and Industry 5.0 will help optimize efficiency, resiliency and sustainability across the complete factory life cycle.
Another huge benefit of Industry 4.0 and 5.0 technological advances are that manufactures can quickly identify the root cause of problems and fix them, mitigating all kinds of threats to the factory’s processes. Manufactures are seeking to increase revenues and often forget to address the “Hidden” challenges.
Addressing your “Hidden Factory” will provide in-depth visibility and critical insight into the processes of the larger manufacturing process. The factory shop floor and all critical processes should be optimized and protected with relevant security controls; making the factory a sustainable environment following the zero trust, zero tolerance and zero waste principle. Addressing the “Hidden Factory” is an ongoing process, done step-by-step. Finding your “Hidden Factory” can boost the transformation to becoming an efficient “Green Factory”!
For more from Solutions Architect Antoinette Hodes, click here. Lastly, discover new trends, expert interviews, and so much more – subscribe to the CyberTalk.org newsletter.